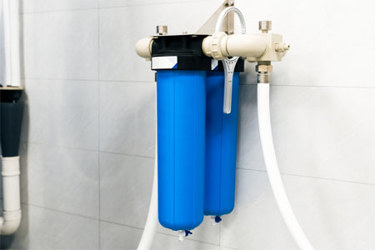
Filtration is a ubiquitous process, integral to a myriad of applications ranging from simple preparative lab-scale tasks to stringent quality controls in large-scale Good Manufacturing Practice (GMP) production. Its versatility allows it to remove life-threatening contaminants, thereby safeguarding patient safety, or facilitating the smooth operation of other processes. Often, filtration is the go-to method for separating desired substances from undesired ones, typically based on size. The unwanted materials can vary widely, from macroscopic solid contaminants to microscopic entities like bacteria, viruses, and complex molecules. Each type of contaminant can significantly impact the process's efficiency or the final product's safety and efficacy.
Filters are generally straightforward to use, often requiring nothing more than fluid input and output. This simplicity makes them easy to integrate into a wide range of processes and procedures. However, the ease of use and the trust built over generations do not imply that filters are unaffected by the evolving demands of the processes they support. As industries advance and processes become more complex, the requirements for filtration systems also evolve, necessitating continuous innovation and adaptation to meet these new challenges.
Access the full article to learn more.